I finally got a chance to get to a shop to install sub-frame braces.
I elected to use 1-1/2" ChromeMoly round tubing(1.9" OD). We made brackets and bolted to the subframe to attach the tubing at the rear and fabricated another pair of brackets up front to bolt to the front subframe.
Here is the tubing fitting on the front subframe.
A slight bend at the back end was needed before we could begin boxing in the rear.
Here, the rear passenger side is complete.
Now it was a simple task to fabricate side plates, drill holes and bolt up the front.
Then the process was completed for the passenger side.
I could tell on the drive home that the chassis was stiffer. Hopefully I'll soon get a chance at the track to see if the car launches better.
I elected to use 1-1/2" ChromeMoly round tubing(1.9" OD). We made brackets and bolted to the subframe to attach the tubing at the rear and fabricated another pair of brackets up front to bolt to the front subframe.
Here is the tubing fitting on the front subframe.
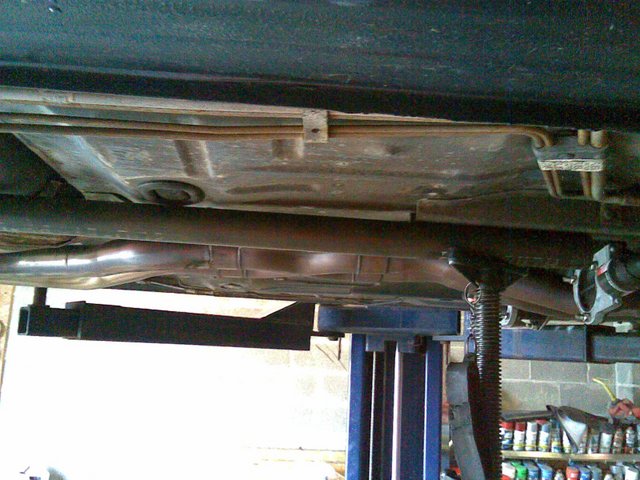
A slight bend at the back end was needed before we could begin boxing in the rear.
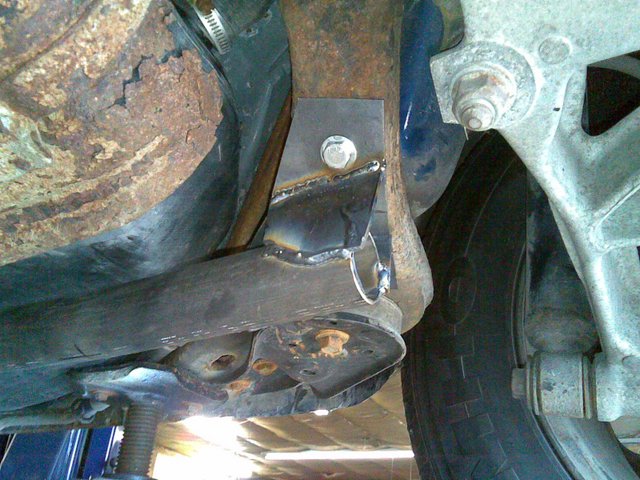
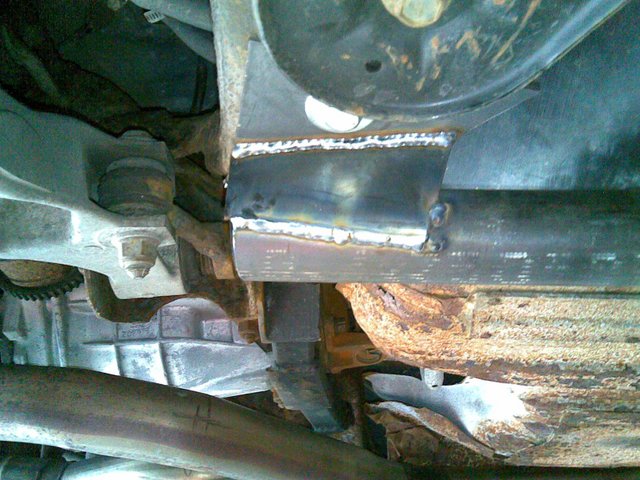
Here, the rear passenger side is complete.
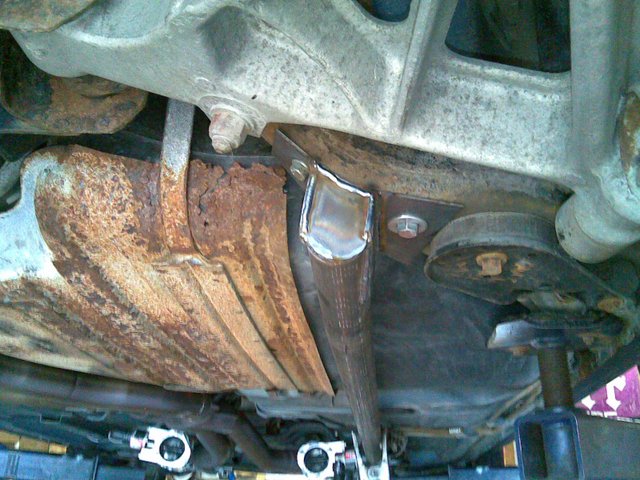
Now it was a simple task to fabricate side plates, drill holes and bolt up the front.
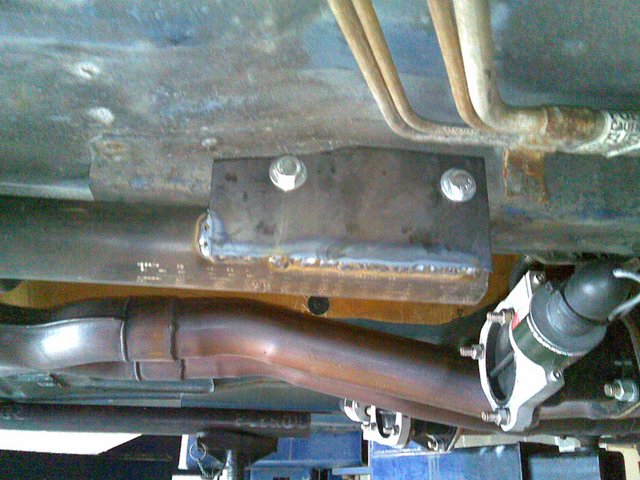
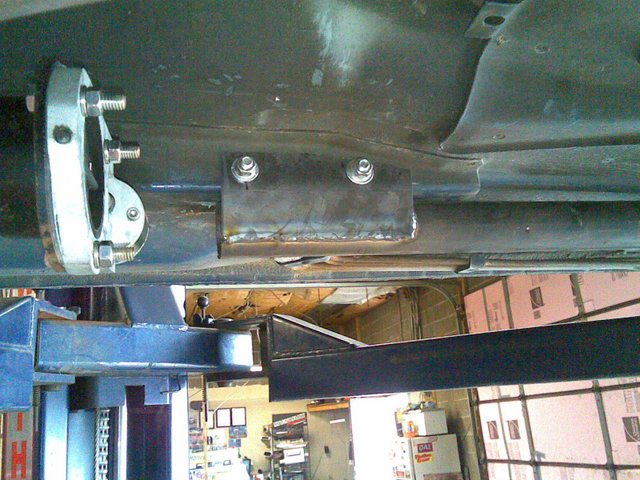
Then the process was completed for the passenger side.
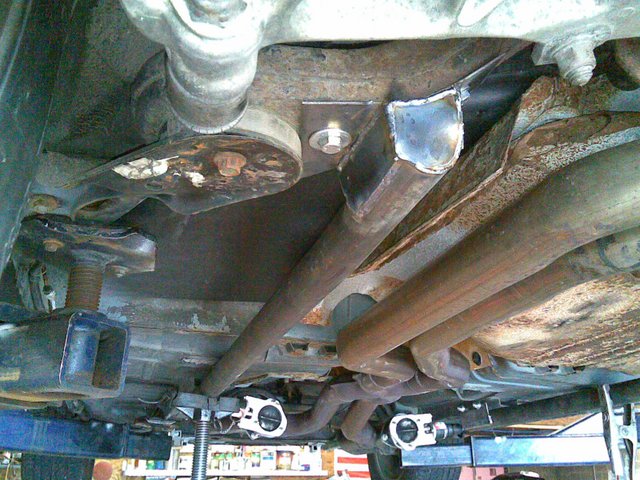
I could tell on the drive home that the chassis was stiffer. Hopefully I'll soon get a chance at the track to see if the car launches better.